球墨铸铁无冒口技术
铸造铁合金罗永涛
关注本作者,请加微信15229357317
**节:球墨铸铁无冒口技术概述
定义:球墨铸铁无冒口技术是指在铸造过程中不使用冒口,通过优化浇注系统设计、采用先进的填充方式和控制技术等手段,实现金属液的稳定充型和补缩,从而减少或消除冒口的使用。
目的:提高铸件质量,降低生产成本,简化生产流程。
第二节:球墨铸铁无冒口技术的实现条件
高品质的铁液:通过提高冶金品质,控制化学成分,改善球化和孕育处理,降低铁液含硫量,适当提高碳量和碳当量,以获得高品质的铁液。
合理的铸件模数:球铁件的平均模数应在一定数值以上(如2.5cm),以确保金属液在凝固过程中的补缩效果。
低温浇注:浇注温度需控制在一定范围内(如不超过1380℃),以减少液态收缩,提高铸件的致密性。
高强度的铸型:使用强度高、刚性大的铸型,并确保铸型上下箱之间的紧固,防止抬箱,保证铸件的尺寸精度和表面质量。
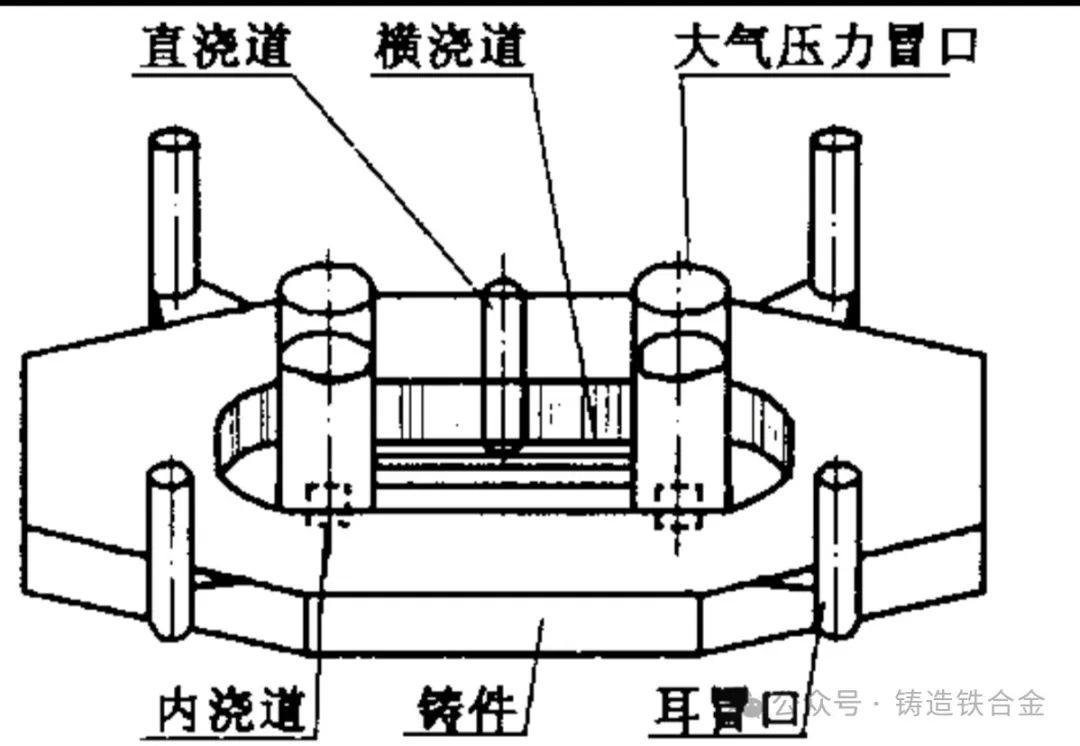
第三节: 球墨铸铁无冒口技术的优点
提高铸件质量:无冒口技术可以减少传统铸造工艺中常见的气孔、夹渣等缺陷,提高铸件的整体质量。
降低生产成本:由于减少了冒口的使用,节省了原材料和能源,同时简化了生产流程,降低了生产成本。
提高生产效率:无冒口技术可以缩短生产周期,提高设备利用率和生产效率。
优化铸件结构:通过精确控制金属液的流动,无冒口铸造能够实现更加合理的铸件结构,减少不必要的金属浪费。
第四节:球墨铸铁无冒口技术的应用
压缩机缸体:在压缩机缸体的铸造过程中,采用无冒口技术可以取消大量的保温冒口套的使用,节约造型工时、清理工时和铁液损耗,同时提高铸件的外观质量和力学性能。
飞轮壳:对于壁厚差较大、结构复杂的飞轮壳铸件,采用无冒口技术可以实现高品质、高出品率的铸造生产。通过严格控制铁液的化学成分、提高铁液的流动性、降低浇注温度等措施,成功生产了柴油发动机球墨铸铁飞轮壳铸件。
无冒口技术生产工艺图
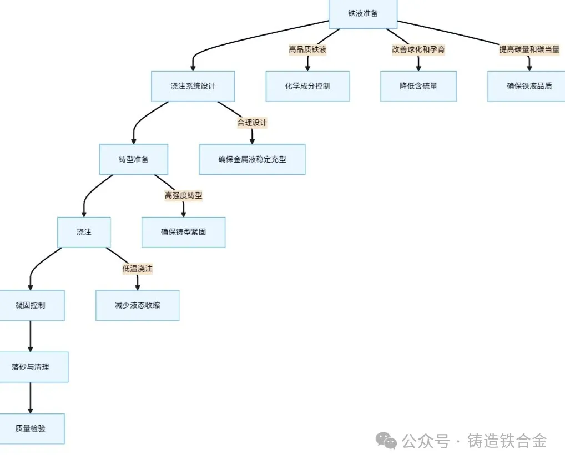
第五节:无冒口工艺的基本原理
无冒口铸造工艺是利用液态金属的流动性,通过精确控制浇口和浇注速度,使金属液能够均匀地充填铸型。
在凝固过程中,利用金属液自身的收缩和石墨化膨胀来补偿铸件的收缩,从而避免传统铸造工艺中冒口的使用。
高温的铁液浇铸之后,体积不断减小,当温度降低到一定之后,球体的体积变化由收缩变为膨胀,在快要凝固终了时,体积的变化又转变为收缩(二次收缩)。随后凝固结束。因此,如果液态金属浇铸时的体积小于凝固终了时的体积就有望得到无缩孔的球铁铸件。所谓无冒口铸造,是根据球铁在适当条件下,从浇铸完毕到凝固终了所发生的总收缩量为零这一原理进行的。
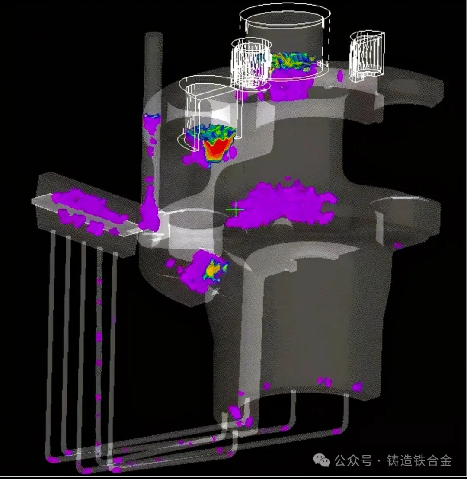
第六节,无冒口生产工艺的关键
1、对液态金属的控制
要生产完好的无冒口铸件,要求液态金属具有良好的石墨化能力和非碳化物形成倾向。为了避免诸如碳化物形成元素或反石墨化元素等有害杂质污染,金属液态使用有的炉料化学成分准确且必须洁净。各种炉料或回炉料必须严格分类储存堆放。
2、化学成分的选择
成分的选择是成功获得无冒口球铁的关键,必须遵从以下原则:
①得到单一铁素体铸态组织,
②在厚大件中防止出现石墨漂浮
③要消除多余的镁及其他反石墨化元素。对于厚大件儿碳当量CE=C+1/3SI要控制在4.4以下。熔化过程中,原铁液中的硅含量要通过加入碳化硅来调节,使其加入量控制在1.0~1.2% 范围内。碳化硅是降低碳化物形成的有效添加剂。
无冒口技术条件的目标成分
碳
3.6%
硅
2.6%
锰
0.35%
磷
0.03%
硫
0.02%
镁
0.045 %
CE
4.6%
3、球化处理过程
过量的镁处理会引起收缩或浮渣缺陷。一般选用6一2球化剂冲入法处理,硅钡孕育剂进行一次孕育处理,再使用硅锶孕育剂进行随流处理。工艺出品率为90%~95%。
4、熔炼温度的控制
熔炼过程中金属过热会形成碳化物,降低凝固过程的体积膨胀。在熔炼时1400°C以下的,调节原铁液化学成分。化学成分调节好后迅速升温,使温度达到出炉温度所需的温度后迅速出炉,出炉温度控制在1500°C左右。
5、浇铸温度
由于在厚大件中,浮渣缺陷出现在铸件的顶部,并形成一个富集区,其厚度可以利用装在铸件底部的超声波探伤器来测量。测得结果表明,无冒口的球铁浮渣区域厚为250mm,浇铸温度越低,浮渣区越厚。浇铸温度不能低于1300°C。
6、球化衰退
衰退了的球铁增加了碳化物形成倾向,降低了石墨球圆整度。处理后高硅(高CE)的情况在 20分钟内没有发现明显的衰退,而低硅(低CE)的情况下,在5分钟之内就出现了衰退。
7、铸型的控制
砂型没有足够的强度会引起球铁的收缩缺陷。采用呋喃树脂砂型来生产球铁,铸件模数越大,膨胀力越大,直径为80mm的铸件**膨胀力为40KGF,无冒口球铁的最小模数为2.5cm(直径大于100mm),其膨胀力远超过呋喃树脂的正常强度25KGF。因此,对于无帽口工艺来说,采用刚性砂箱套在砂型外是必须的。
第七节:球铁飞轮壳的无冒口铸造工艺
1、工艺分析
1.1、铸件简介
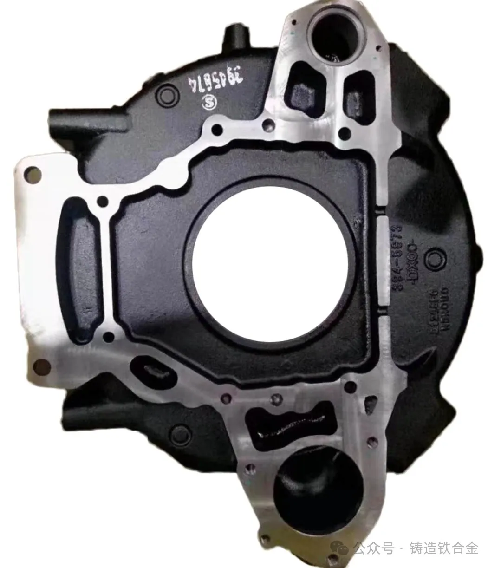
汽车发动机上的飞轮壳毛坯,材质是QT450-10,重65kg。该铸件结构比较复杂,壁厚差比较大,薄的部位为8mm,较厚处达30mm,多且分散,极易产生缩孔、疏松等缺陷;外形结构复杂,砂芯制作困难,尺寸难以控制;铸件采用球墨铸铁,极易产生球化不良和夹渣缺陷。
1.2、无冒口工艺的可行性
该铸件的壁较薄,且壁厚不均匀,要求铸件表面无气孔、砂眼等缺陷,内部组织致密、无缩孔缩松缺陷,试棒的抗拉强度不得低于QT450-10 的标准。若采用传统的浇冒口补缩的球墨铸铁生产方法,需要补缩的部位多且分散,造成工艺出品率低,而且易出现缩孔缩松等缺陷,无法满足要求。
铁液的特性:球墨铸铁件,从铁液浇人铸型开始,随铁液温度下降就会产生收缩,称之为液态收缩;若凝固时产生奥氏体,还会产生凝固收缩;在液态或凝固时析出石墨球,由于石墨的密度只有奥氏体的三分之一左右,就会产生体积膨胀。所以,若液态降温时的体积收缩量与凝固时的体积收缩量之和小于石墨化膨胀的体积增加量,即可实现球铁件的无冒口铸造生产。
采用高刚度的铸型,能够在铁液的进出口凝固封闭后,型腔尺寸保持不变。在不发生石墨漂浮的前提下,采用尽可能高的碳当量,适当的孕育,确保充分石墨化,**限度地增大石墨化膨胀的体积增加量。
采用多道内浇道,使铁液分散进入型腔,并配合冷铁调节,尽可能使铸件各部位同时开始、并同步进行冷却和凝固。
大量使用冷铁,强化铸件冷却,使铁液进入型腔后,铸件外层迅速冷却、凝固,在内浇道及铸件心部的液态通道凝固封闭之前提早完成一部分收缩,形成体积空缺,及时从液态通道获取补缩液体,增大内浇道的流量(即增大外部补缩量),提高浇注系统的补缩效果。
适当降低浇注温度,减少液态体积收缩。该铸件壁较薄,必须增强铁液的流动性。
2、工艺设计
2.1、成分分析
为保证铸造性能,将CE 选择在共晶成分左右,此时铁液的流动性能**,形成集中缩孔的倾向大,铸件组织的致密度高。由于铸件较薄,CE 过高时产生石墨漂浮的倾向小,故CE 的选择在共晶点附近,即4.6%~4.7%(由于球化元素的存在,球铁的共晶点已移至4.6%~4.8%附近)。
Si 能促进石墨化、增加铁素体含量、细化石墨、强化基体组织,但Si 提高韧性和脆性转变温度,降低冲击韧性。因此,在选定高碳当量的前提下应采用高C 低Si 的原则,最终确定将Si 含量控制在2.6%~2.8%较合适。
P 含量偏高,使凝固范围扩大,同时低熔点磷共晶在最后凝固时得不到补给,并且使铸件外壳变弱,因此有增大缩孔、缩松产生的倾向,故P 含量应控制在小于0.03%。
RE 残余量过高会恶化石墨形状,降低球化率,因此RE 含量不宜太高。而Mg 又是一个强烈稳定碳化物的元素,阻碍石墨化。残余Mg 含量及残余RE 量过高会增加球铁的白口倾向,使石墨膨胀减小,另外当它们的含量较高时,会增加缩孔、缩松倾向,故残留Mg 含量和RE 含量不宜过高。
最终确定铁液的成分为:
CE
4.6%~4.8%
C
3.6%—3.8%
Si
2.6%~2.8%
MN
≤0.4%、
P
≤0.03%、
S
≤0.02%、
Mg残
0.025%~0.040%
RE残
0.020%~0.030%
2.2、浇注系统
采用无冒口工艺浇注球墨铸铁,用尽量低的温度在尽量短的时间内充满铸型,且充型平稳。低温、底注、平稳充型是保证球铁飞轮壳铸件品质的基本条件,设计浇注系统的核心是控制内浇道的充型速度。
用了半封闭式浇注系统
ΣF 直:ΣF 横:ΣF 内=1.5:2.0:1.0,
其中横浇道和内浇道一分为四,呈十字形,铁液由铸件中部分散注入铸型,铁液进入铸型更加均匀。
经计算,
ΣF 直=240px2,
ΣF 横=430px2,
ΣF 内=160px2。
采用中间底注、铁液分散进入型腔,整个浇注过程中铁液的流程最短,可缩短浇注时间,浇注过程中铁液温降最小,可以**限度的降低浇注温度,浇注温度初步确定为(1,380±10)℃。
2.3、辅助设计
由于采用呋喃树脂自硬砂造型,而树脂具有一定的发气量,为了避免气孔等缺陷,在铸件四角处分别设有出气孔,用以排气、集渣,同时可以改善铁液的充型状态和作为铁液注满的标志。
3、生产过程
采用呋喃树脂自硬砂造型、制芯,1t 中频感应电炉熔炼,分两包浇注,每包6 件,铁液出炉温度为1,520~1,540℃,浇注温度为(1,380±10)℃。
采用FeSi Mg6RE2 球化剂、包内冲人,加入量为1.2%。
一次孕育剂为硅钡:其中Ba3一3.5%,加入量为0.6%。
随流孕育剂为硅锶:Sr0.8-1.0%,加入量为0.15%。
铸件的球化级别为2级,化学成分(质量分数)为:
C
3.74%
Si
2.65%
Mn
0.35%
P
0.03%
S
0.02%
Mg残
0.035%
RE残
0.023%
按以上工艺生产飞轮壳铸件,经机加工后均未发现缩孔、缩松、气孔等铸造缺陷,试棒
抗拉强度为
510.6MPa,
伸长率为
18.4%,
硬度为
HB186,
工艺出品率为
97.5%。
铸件表面质量、力学性能及内在质量等均满足技术要求。